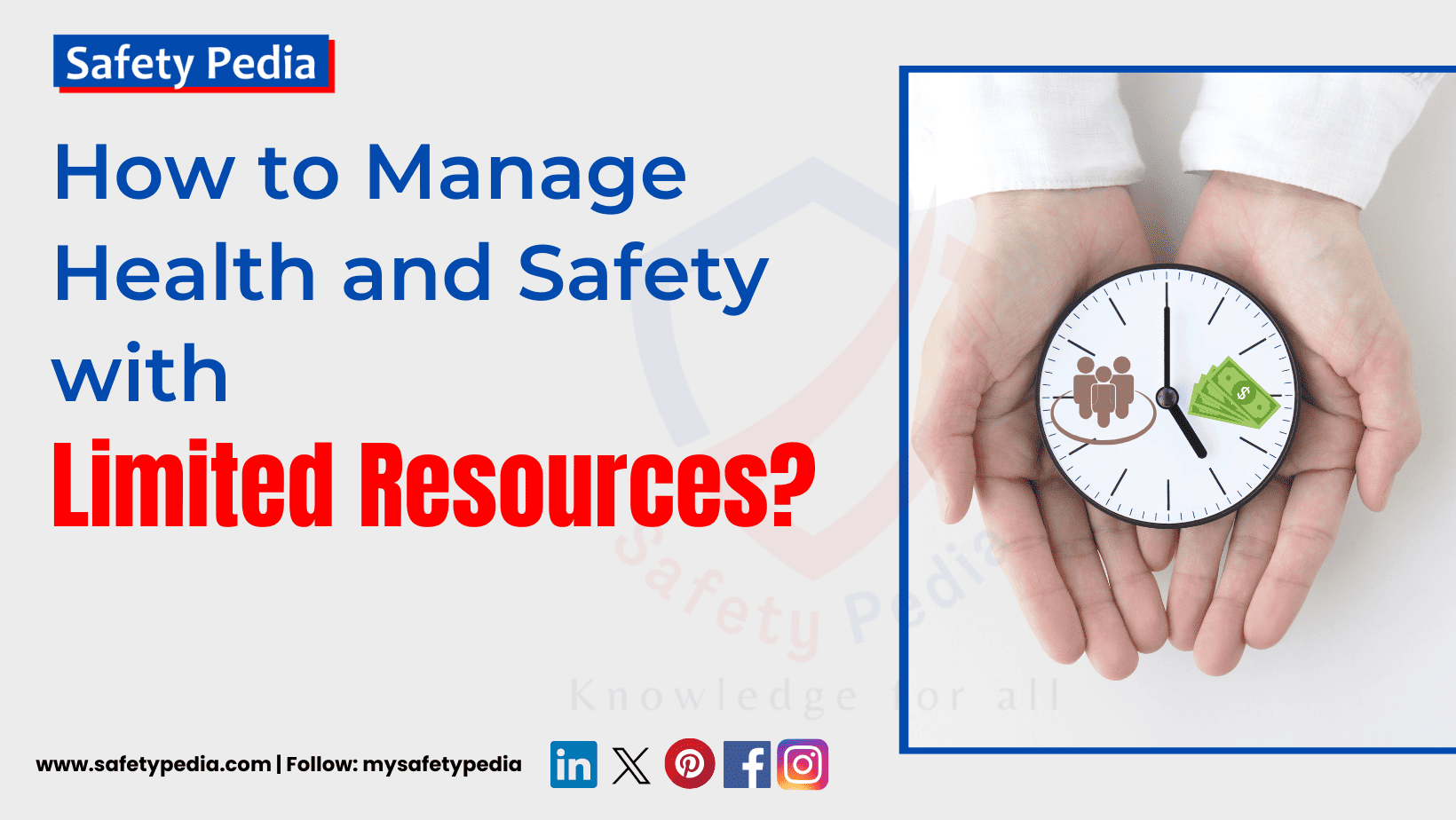
Introduction:
Health and safety is a vital aspect of any workplace, as it protects the well-being of workers, customers, and the public. It’s an essential aspect of every organization, regardless of size or industry. It also benefits businesses by reducing costs, improving productivity, enhancing reputation, and complying with legal obligations.
However, managing health and safety can be challenging, especially when resources are scarce. In this article, we will explain why health and safety is important for businesses, identify the challenges of managing health and safety with limited resources, and provide some tips on how to overcome them.
Why is health and safety important for businesses?
Health and safety is not only a moral duty but also a smart business decision. Here are some of the benefits of having a good health and safety culture in your organization:
- Improved productivity: By providing a safe and healthy work environment, you can boost the morale, motivation, and performance of your employees. You can also reduce absenteeism, turnover, and recruitment costs. A happy and healthy workforce is more efficient, creative, and loyal.
- Reduced costs: By preventing accidents, injuries, illnesses, and damages, you can save on medical expenses, compensation claims, legal fees, fines, repairs, and replacements. You can also avoid losing revenue due to downtime, delays, disruptions, or loss of customers.
- Worker Well-being: The primary reason for prioritizing health and safety is the well-being of employees. A safe workplace reduces the risk of accidents and injuries, ensuring employees return home unharmed.
- Enhanced reputation: By demonstrating your commitment to health and safety, you can improve your image and credibility among your customers, suppliers, partners, regulators, and the public. You can also attract and retain more talent, as well as more business opportunities. A good reputation is a valuable asset that can give you a competitive edge.
- Legal compliance: By following the relevant health and safety laws and regulations, you can avoid penalties, sanctions, or lawsuits that could jeopardize your business. You can also meet the expectations and requirements of your stakeholders, such as investors, insurers, auditors, or customers. Legal compliance is a minimum standard that you should aim to exceed.
- Stay updated on relevant health and safety regulations.
- Focus on essential compliance requirements to avoid fines or legal issues.
What are the challenges of managing health and safety with limited resources?
Managing health and safety can be especially challenging when resources are limited, often due to economic downturns and budget cuts. Safety professionals may face difficulties such as:
- Lack of funds: Safety professionals may have to work with a tight budget, limiting their ability to invest in equipment, technology, training, or external support. They may also have to justify their spending and demonstrate the return on investment of their health and safety initiatives. Having less money means having less equipment, materials, tools, or technology to ensure health and safety standards. It also means having less training, education, or awareness programs to improve health and safety knowledge or culture.
- Lack of time: Safety professionals may juggle multiple tasks and responsibilities, such as conducting risk assessments, developing policies and procedures, providing training and awareness, monitoring performance, reporting incidents, and implementing corrective actions. They may also deal with competing priorities and deadlines and respond to urgent issues or emergencies.
- Lack of staff: Safety professionals may have to work with a small or understaffed team, affecting their workload, capacity, and morale. They may also have to rely on other employees or managers to perform health and safety tasks or roles, which may require additional training, supervision, or communication. Having fewer employees means having less time, skills, knowledge, or experience to deal with health and safety issues. It also means having more workload, stress, or fatigue that could affect the quality of work or increase the risk of errors or accidents.
- Lack of support: Safety professionals may have to deal with a lack of senior management commitment or involvement in health and safety matters. They may also face resistance or indifference from other employees or stakeholders, who may not see the value or importance of health and safety. Having less support from senior management or other departments means having less authority, influence, or resources to implement health and safety policies or practices.
- Dynamic regulatory environment: Safety professionals may have to cope with a complex and dynamic regulatory environment, which may require them to keep updated with the latest laws, standards, and best practices. They may also have to deal with new or emerging risks or hazards, requiring them to conduct research, analysis, or testing.
These challenges can pose significant risks to the health and safety performance of the organization, as well as to the well-being and satisfaction of the safety professionals themselves. Therefore, safety professionals must find ways to manage health and safety with limited resources effectively and efficiently.
Way Forward for Safety professionals?
Safety professionals play a pivotal role in ensuring workplace health and safety, even with limited resources. Economic downturns or budget cuts can lead to reduced staff, training budgets, equipment, and external support. This requires safety professionals to adapt and find innovative solutions to maintain a high level of safety performance while adhering to legal compliance.
- Start small: Don’t try to implement too many changes at once. Start by addressing the most critical hazards and risks.
- Get creative: Explore low-cost or no-cost ways to improve health and safety.
- Collaborate: Communicate effectively with senior management and stakeholders to secure buy-in and support.
- Be patient. It takes time to build a culture of safety.
- Engage: Promote a positive safety culture and involve employees in finding solutions.
- Seek Support: Look for external resources and collaborate with other organizations.
Effectively managing health and safety with limited resources requires a strategic approach. By finding answers to the following questions, safety professionals can ensure workplace well-being while upholding professional standards and ethics:
- How can you prioritize health and safety activities and focus on the most critical risks?\
- How can you leverage existing resources and optimize their use?
- How can you communicate effectively with senior management and other stakeholders to secure buy-in and necessary support?
- How can you promote a positive safety culture and engage your workforce in safety initiatives?
- How can you seek external support and collaborate with other organizations to maximize resources and knowledge sharing?
When resources are limited, prioritize safety measures using a “worst-first” basis approach, according to the hazard ranking priorities (risk) This means focusing on hazards with the highest risk levels, as identified during your hazard identification and assessment process.
As a safety professional, one of your responsibilities is to plan and implement safety programs and interventions to prevent or reduce injuries, illnesses, and losses in your organization. However, you may encounter various resource constraints limiting your ability to achieve your safety goals.
Important Note: Even with limited resources, employers have a legal and ethical obligation to protect workers from all recognized, serious hazards.”
Effective Safety Management in Resource-Limited Environments
Assessing Resource Constraints
Assessing resource constraints is a critical first step in ensuring the effectiveness of health and safety measures in any organization. It’s essential to thoroughly assess resource constraints and identify the limitations that might impact health and safety within your organization. By doing so, you can develop strategies to address these constraints and still maintain a high level of safety.
Resource constraints are factors that restrict the availability or quality of the resources that you need to carry out your safety activities. Resources can include money, time, staff, equipment, materials, information, and support from management and stakeholders. Resource constraints can affect your ability to design, execute, monitor, and evaluate safety programs and interventions.
To assess your resource constraints, you need first to identify the resources that are essential for your safety activities. You can use tools such as a logic model or a work breakdown structure to map out the inputs, outputs, outcomes, and impacts of your safety activities. Then, you need to estimate the amount and quality of each resource that you need and compare it with the amount and quality of each resource that you have or can access. This will help you identify any gaps or shortfalls in your resources.
Identifying Limited Resources
Financial limitations
Financial constraints are a common challenge for safety professionals. When budgets are limited, it can affect your ability to invest in necessary safety equipment, training, or facility improvements. To address this limitation, it’s crucial to prioritize safety initiatives and allocate funds strategically. Look for cost-effective solutions and make a strong business case for safety investments to secure the necessary funding.
You may have a limited budget to spend on your safety activities or face difficulties securing funding from internal or external sources. This can affect your ability to purchase equipment, materials, training, or services necessary for your safety programs and interventions.
Staffing constraints
Staffing limitations, such as a shortage of safety professionals, can make it difficult to manage and enforce safety protocols effectively. To address this challenge, focus on cross-training existing personnel and delegating safety responsibilities. Encourage all employees to become safety-conscious, creating a culture where everyone plays a part in maintaining a safe workplace.
You may have a limited number of staff who are qualified, trained, or available to perform your safety activities. This can affect your ability to assign roles and responsibilities, delegate tasks, supervise work, and ensure quality and compliance.
Time limitations
Time constraints can hinder comprehensive safety efforts. When time is scarce, it’s important to streamline safety procedures, prioritize essential tasks, and establish efficient workflows. Regularly review and update safety protocols to ensure they remain relevant and achievable within the given time frame. Automation and technology can also be leveraged to save time in safety reporting and compliance tracking.
You may have a limited amount of time to complete your safety activities, or face competing demands from other projects or priorities. This can affect your ability to plan, implement, monitor, and evaluate your safety programs and interventions in a timely manner.
Understanding the Impact of Limited Resources
As a safety professional, it’s vital to understand the profound impact that resource limitations can have on safety within an organization. Here, we’ll explore the consequences of resource constraints, their effects on safety initiatives, and the imperative for a strategic approach:
The consequences of resource limitations
Resource limitations can have profound consequences for safety management within an organization. When resources, such as finances, staffing, and time, are scarce, the potential consequences include:
- Increased risk of accidents, injuries, and illnesses: Scarce resources can lead to a higher risk of accidents and incidents. For instance, lack of funding for necessary safety equipment or maintenance can result in equipment failures, potentially leading to human suffering, loss of life, disability, absenteeism, turnover, compensation claims, legal fees, fines, and penalties.
- Reduced Preparedness: Limited resources can impede an organization’s preparedness for emergencies and crises. Inadequate training or insufficient emergency response equipment can hamper the ability to respond effectively to unexpected events. If you do not have a plan to deal with potential hazards and emergencies, you may not be able to respond quickly and effectively when they occur. This can lead to more damage, disruption, and losses for your business. For example, if you do not have a fire evacuation plan or fire extinguishers in your workplace, you may be unable to prevent or control a fire outbreak.
- Reduced compliance with legal and other requirements: Failure to meet safety regulations due to resource constraints can lead to legal liabilities and financial penalties. Non-compliance can result in costly lawsuits, fines, and reputational damage. If you do not comply with the health and safety laws and regulations that apply to your business, you may face legal action from the authorities or other parties. You may also lose your license, certification, accreditation, or contract with your customers or suppliers. For example, if you do not provide adequate personal protective equipment (PPE) for your workers who handle hazardous substances, you may violate the Occupational Safety and Health Act (OSHA) or other relevant standards.
- Damaged reputation and customer satisfaction: Resource limitations can have a direct impact on an organization’s reputation and, subsequently, customer satisfaction. If you do not manage health and safety effectively, you may lose the trust and confidence of your customers, suppliers, investors, partners, and the public. You may also damage your brand image and reputation in the market. For example, if you do not ensure the hygiene and quality of your food products, you may cause food poisoning or contamination for your customers.
- Decreased employee engagement and morale: Limited resources can lead to an overburdened workforce, causing stress and frustration among employees. This, in turn, can negatively affect morale, motivation, and, ultimately, safety culture. Insufficient investment in safety can negatively impact employee morale and job satisfaction. Workers may perceive a lack of care for their well-being, leading to reduced job satisfaction and potentially high turnover rates. If you do not manage health and safety effectively, you may demotivate and disengage your workers. You may also lower their morale, satisfaction, loyalty, commitment, productivity, and quality. For example, if you do not provide a safe and healthy work environment for your workers, you may cause them stress, fatigue, burnout, or dissatisfaction.
- Lowered productivity and quality: Resource limitations can also impact an organization’s internal operations, particularly in productivity and quality. If you do not manage health and safety with limited resources, you may compromise the performance of your business. You may have more downtime, delays, errors, or defects in your products or services. You may also have higher costs due to compensation claims, legal fees, repairs, or replacements.
How it affects safety initiatives
Resource limitations can also affect your ability to implement and maintain effective safety initiatives. Resource limitations can have several adverse effects on safety initiatives:
- Reduced Implementation of Safety Programs: Limited resources often lead to a reduction in the number and effectiveness of safety programs. These programs may be postponed, scaled down, or altogether abandoned, making it difficult to address safety risks comprehensively. Limited financial resources can curtail the implementation of safety programs and the purchase of essential safety equipment. This can compromise the effectiveness and quality of your safety programs and increase the risk of accidents or injuries.
- Inadequate Training: Budget constraints may limit the ability to provide comprehensive safety training to employees, potentially leaving them ill-prepared to handle safety issues. This affects the competency of employees in handling safety procedures and protocols, potentially leading to higher incident rates and a compromised safety culture. You may be unable to provide adequate training to your employees, contractors, or other stakeholders on health and safety topics due to a lack of time, money, or expertise. This can affect their awareness, knowledge, skills, and attitudes towards health and safety and reduce their compliance and performance.
- Time Pressure: Time limitations can result in a rushed approach to safety, potentially compromising the quality of safety assessments and protocols. Limited resources can create time pressure for safety professionals, making it challenging to conduct thorough safety assessments, investigations, and preventive measures. Rushed decisions can increase the chances of overlooking critical safety issues. You may have to deal with tight deadlines, multiple tasks, and competing priorities, creating stress and fatigue for you and your team. This can affect your decision-making, communication, and problem-solving abilities and increase the likelihood of errors or oversights.
- Reduced Safety Program Scope: A lack of resources may force safety initiatives to focus on a narrow range of hazards or compliance requirements only and reduce the scope of safety programs and initiatives. This limited scope can leave other safety concerns unaddressed, leaving the workplace vulnerable to hidden dangers. You may have to limit the scope of your safety program to focus on the most critical or urgent issues due to resource limitations. This can result in neglecting some important aspects of health and safety, such as prevention, evaluation, improvement, or innovation.
- Delayed Response to Hazards: Resource limitations can delay responding to identified safety hazards. The time lag between hazard identification and corrective action increases the potential for accidents and injuries, as well as regulatory non-compliance. Insufficient resources can slow down the response to identified safety hazards, leaving employees exposed to risks for extended periods. You may be unable to respond quickly or effectively to hazards that arise in your workplace due to insufficient resources or capabilities.
- Resource Allocation Challenges: Deciding how to allocate limited resources can become a complex task for safety professionals in scarce resource environments. Balancing immediate needs with long-term safety goals can be a struggle. Misallocating resources can lead to inefficiencies and missed opportunities for hazard prevention. Safety professionals may face difficult decisions in allocating limited resources. They must prioritize critical safety measures while postponing less urgent tasks, which can be a complex and delicate. You may have to make difficult decisions on allocating your limited resources among different health and safety needs, goals, or activities. This can create conflicts, trade-offs, or compromises that affect your safety outcomes and performance.
Strategic Planning
Health and safety management is a crucial aspect of any organization, but it can be challenging to implement and maintain when resources are limited. However, this does not mean health and safety management should be neglected or compromised.
Goal Setting
The first step in drafting a safety strategic plan is to set clear and achievable health and safety goals.
Setting achievable health and safety goals
Prioritize goals that directly address the most significant risks identified in the assessment. These goals should be specific, measurable, attainable, relevant, and time-bound (SMART). They should also align with the organization’s vision, mission, values, and objectives. Involve key stakeholders, such as employees, safety committees, and management, in the goal-setting process to gain buy-in and support.
Aligning goals with available resources
Once you have set your health and safety goals, you need to assess your available resources and align them with your goals. Resources can include financial, human, physical, and technological assets. You need to:
- Assess the resources available for safety management, including budget, personnel, and time. Check how much of each resource you have, how much you need, and how you can allocate them effectively.
- Ensure that the selected goals align with the resources at hand. If resource constraints are significant, prioritize a limited number of high-impact goals over a broad but shallow approach.
- Consider innovative, cost-effective solutions and leverage existing resources efficiently to maximize the impact of your safety initiatives.
Some questions to ask yourself are:
- What are the current and projected costs of health and safety initiatives?
- How many staff members are dedicated to health and safety tasks?
- What equipment, tools, software, or data do you have or need for health and safety purposes?
- How can you leverage existing or external resources to support your health and safety goals?
Resource Allocation
After aligning your goals with your resources, you need to allocate your resources based on your priorities. This means you must decide which health and safety initiatives are more urgent, important, or impactful than others.
Allocating resources based on priorities
- Prioritize safety risks based on their potential severity and likelihood of occurrence. Focus on addressing the most critical risks first.
- Allocate resources proportionally to the prioritized goals. Ensure that the allocation aligns with the identified risks.
- Periodically review and adjust resource allocation as the organization’s safety needs evolve.
Making the most of limited resources
Finally, you need to maximize your limited resources by optimizing their use and minimizing waste. This means that you need to find ways to increase the efficiency, effectiveness, or value of your resources. Some strategies to consider are:
- Emphasize preventive measures to reduce the demand for reactive resources.
- Encourage a culture of safety where employees actively participate in identifying and mitigating risks.
- Seek opportunities for resource sharing, cross-training, and knowledge transfer among employees to enhance the effectiveness of your safety efforts.
- Streamlining processes or procedures to reduce duplication or redundancy
- Automating tasks or functions to save time or money
- Seeking grants, subsidies, or sponsorships to supplement your budget. Explore government grants or local resources that may provide funding for safety initiatives.
Timeline and Milestones
The last step in drafting a safety strategic plan is to establish a realistic timeline for your initiatives and create milestones to track your progress. A timeline is a schedule that outlines when each initiative will start and end, who will be responsible for it, and what resources will be required for it. A milestone is a significant event or achievement that marks the completion of a phase or a goal. Some tips for creating a timeline and milestones are:
Establishing a realistic timeline for initiatives
- Develop a clear and realistic timeline for the implementation of safety initiatives. Take into account the scope and complexity of each goal.
- Ensure the timeline allows for adequate planning, execution, and evaluation of each initiative. Avoid setting overly aggressive deadlines that may compromise safety quality.
Creating milestones to track progress
- Break down larger or complex safety initiatives into smaller, measurable milestones.
- Regularly assess progress and track performance against these milestones. This allows for early identification of potential issues or adjustments needed.
- Communicate the timeline and milestones to all relevant parties. Involve key personnel and stakeholders in milestone reviews to maintain transparency and accountability.
- Monitor the timeline and milestones regularly and adjust them as needed
- Celebrate the milestones and recognize the achievements
Employee Training
Developing cost-effective training programs
- Begin by conducting a training needs assessment to identify the most critical areas where employee training is required. Focus on addressing the highest-priority safety risks.
- Leverage technology and e-learning platforms to develop cost-effective training materials. These can be reused and easily updated, reducing training costs.
- Consider creating in-house training content and materials to minimize external training expenses.
Ensuring employees are well-informed
- Communicate the importance of safety to all employees. Promote a culture of safety awareness where everyone understands their role in maintaining a safe workplace.
- Implement a “train-the-trainer” approach, where a select group of employees become trainers for their peers, reducing the need for external trainers.
- Regularly review and update training materials to inform employees about the latest safety practices and regulations.
Skill Development
Identifying essential skills for the team
- Collaborate with key stakeholders, including safety committees and department heads, to identify the essential safety skills required within your organization.
- Prioritize skills that directly address the most significant safety risks or compliance needs.
Investing in skill development within constraints
- Explore free or low-cost training resources, such as webinars, online courses, and open educational resources, to enhance employee skills.
- Cross-train employees to have a broader skill set. This can be particularly valuable when facing resource constraints, as it allows for greater flexibility in resource allocation.
- Consider establishing mentorship programs within the organization, where experienced employees can guide and develop the skills of newer or less-experienced team members.
Competence development
Assessment and Measurement:
- Implement a system to assess and measure employee competence in safety-related skills. This could include written tests, practical assessments, or on-the-job evaluations.
- Regularly review and update competency standards to align with changing safety requirements and industry best practices.
Feedback and Improvement:
- Encourage employees to provide feedback on the effectiveness of training programs and their skill development experiences.
- Use this feedback to continually improve training content and methods to make the best use of available resources.
Recognize and Reward Competence:
- Acknowledge and reward employees who demonstrate competence in safety-related skills. This can motivate other employees to invest in their own skill development.
- Consider establishing a system of recognition or certification for employees who achieve specific safety competence levels.
Prioritizing Health and Safety
A limited resource environment is one where there is a scarcity of material, human, or financial resources to meet the needs and demands of the work. Prioritizing health and safety in a limited resource environment is crucial to ensure the well-being of employees and maintain regulatory compliance.
Risk Assessment
Risk assessment is a process of evaluating the potential hazards and consequences of an activity, event, or situation. When dealing with limited resources for safety management, risk assessment becomes a crucial component. It can help to allocate scarce resources for safety management.
Identifying critical risks
The first step is to identify the most significant risks that your organization faces based on the likelihood and severity of their impact. You can use various tools and methods, such as brainstorming, checklists, surveys, inspections, audits, incident reports, etc. You should also consult with your stakeholders, such as employees, customers, suppliers, regulators, etc., for their input and feedback. Identifying critical risks that pose the most serious threat to the health, safety, or environment of the people, property, or operations involved.
Once you have identified the critical risks, you should prioritize them according to their urgency and importance. Prioritize risks based on their potential for severe consequences, such as fatalities or serious injuries, and their likelihood of occurrence.
- Identify the most critical health and safety risks in your workplace.
- Focus your limited resources on addressing these high-priority risks first.
Ranking risks based on severity and likelihood
Once critical risks are identified, the next step is to generate possible control measures for each critical risk based on the hierarchy of controls. Develop cost-effective solutions for minimizing these hazards. The hierarchy of controls is a widely accepted framework that ranks the effectiveness of different types of controls, from elimination (the most effective) to personal protective equipment (the least effective).
It would be best if you aimed to implement the highest level of control that is reasonably practicable, considering the cost, feasibility, availability, and suitability of the control measure. You should also evaluate the benefits and drawbacks of each control measure, such as its impact on productivity, quality, customer satisfaction, compliance, etc. You should then select the most cost-effective control measure for each critical risk, considering the available resources and the expected return on investment. Allocate your limited resources to address the highest-priority risks first.
Regular Audits
In essence, while managing safety within limited resources, regular audits should be strategic and outcome oriented. They should help pinpoint critical areas for improvement and optimize the use of available resources for enhanced safety without unnecessary financial burden.
- Periodically Internal Audit Your Health and Safety Programs. Despite resource constraints, the importance of regular internal safety audits cannot be overstated. Conduct focused audits to prioritize high-risk areas and ensure that limited resources are utilized where they are needed most.
- Make Adjustments Based on the Findings. When conducting audits, focus on actionable findings that can lead to tangible improvements. Prioritize addressing issues that have the most significant impact on safety and resource utilization. Provide cost-effective solutions to safety programs based on audit results. Leverage internal expertise and find creative solutions that don’t strain the budget.
Optimizing Safety Equipment Investments in a Resource-Constrained Environment:
By optimizing your approach to safety equipment investments, you can maintain a high level of safety within limited resources. This strategy not only enhances workplace safety but also contributes to cost savings and resource efficiency.
Prioritize Essential Safety Equipment:
- Focus on acquiring and maintaining essential safety equipment that directly addresses high-priority risks within your organization.
- Avoid purchasing costly gadgets or equipment with limited practical applications for your safety needs.
Cost-Efficient Procurement:
- Explore cost-efficient procurement options, such as bulk purchasing or negotiating with suppliers for discounts.
- Consider leasing or renting safety equipment for tasks that don’t require continuous use.
Lifecycle Cost Consideration:
- When evaluating safety equipment options, consider the total cost of ownership, which includes not just the purchase price but also maintenance and replacement costs.
- Opt for durable equipment that may have a higher upfront cost but offers long-term cost savings due to reduced maintenance and replacement needs.
Legal and Regulatory Compliance
Safety management is a crucial aspect of any business, but it can be challenging to implement and maintain when you have limited resources. However, this does not mean that you can ignore or neglect your legal and regulatory obligations. Therefore, develop strategies to help you understand and prioritize your compliance efforts, while ensuring the safety of your employees, customers, and stakeholders.
Understanding legal obligations
The first step to effective safety management is to understand your legal obligations. Depending on your industry, location, and size, you may be subject to different local laws, international laws and regulations that govern how you should manage safety risks in your workplace. You should also keep yourself updated on any changes or updates to the laws and regulations that may affect your business.
- Laws and Regulations: Conduct thorough research of the applicable laws and regulations for your business. Identify and familiarize yourself with relevant local, national, and international laws and regulations that pertain to workplace safety. This includes occupational safety laws, environmental regulations, and industry-specific standards. You can use online resources, such as government websites, databases, or publications, to find relevant information.
- Compliance Requirements: Clearly outline the specific compliance requirements imposed by these laws and regulations. Understanding what is legally mandated is essential to avoid penalties, legal issues, and reputational damage.
- Safety Standards: Stay updated on industry safety standards, best practices and cost-effective safety solutions. These can provide valuable guidance for achieving compliance and maintaining a safe workplace.
- Expert Advice: When in doubt about your legal obligations, consult with legal experts, industry associations, or other professionals who can advise you on your specific requirements. They can provide valuable insights into the legal aspects of safety compliance.
For example, you may need to comply with the Occupational Safety and Health Act (OSHA), the Environmental Protection Agency (EPA), the Food and Drug Administration (FDA), or other federal, state, or local agencies. You may also need to follow industry-specific standards or guidelines, such as those issued by the National Fire Protection Association (NFPA), the American National Standards Institute (ANSI), or the International Organization for Standardization (ISO).
Prioritizing compliance efforts
Once you have identified your legal obligations, you should prioritize your compliance efforts to meet at least the minimum regulations. This means that you should focus on the most critical and urgent safety issues that pose the highest risk to your business and stakeholders. You should also consider the potential consequences of non-compliance, such as fines, penalties, lawsuits, or reputational damage.
To prioritize your compliance efforts, you should conduct a risk assessment of your workplace, as stated above. You should also identify the existing controls or measures that you have in place to mitigate or eliminate the risks. Based on your risk assessment, you should develop a safety plan that outlines the actions and resources that you need to take to comply with the regulations. You should also monitor and review your safety plan regularly to ensure its effectiveness and suitability.
Allocate your limited resources strategically. Focus on addressing the high-priority risks that are directly related to legal obligations. This may include investing in necessary safety equipment, providing required training, and implementing specific safety measures. Look for cost-effective ways to meet compliance requirements.
By focusing on the most critical risks and minimum regulatory requirements, organizations can mitigate legal and financial risks, maintain compliance, and work towards a safer workplace, even when resources are scarce.
Promote Safety Culture, Communication and Collaboration
Communication and collaboration are essential for promoting a safety culture, sharing best practices, identifying hazards, implementing solutions, and monitoring outcomes. In this blog post, we will discuss some of the strategies and benefits of communication and collaboration for safety management with limited resources.
Promoting a Safety Culture
One of the first steps to improve safety performance is to promote a culture of safety awareness among all employees, managers, and leaders. A safety culture is a set of values, beliefs, attitudes, and behaviors that support safety as a priority and a responsibility for everyone. A safety culture can help reduce accidents, injuries, illnesses, and costs, as well as increase productivity, quality, and morale.
Promoting a culture of safety awareness
- Encourage a culture where safety is a top priority for everyone. Emphasize that safety is not just a task but a core value of the organization.
- Utilize frequent safety reminders, posters, and digital displays to keep safety at the forefront of employees’ minds.
- Communicate the vision, mission, goals, and policies of your organization regarding safety. Make sure everyone understands the importance and benefits of safety for themselves, their colleagues, their customers, and their organization.
- Incorporate safety topics into regular team meetings and discussions, demonstrating its importance.
- Empower them to take ownership and initiative for safety in their work areas. Recognize and celebrate their contributions and achievements.
- Promote a culture where safety is ingrained into daily routines. Encourage employees to view safety as a personal responsibility.
- Use visual cues such as safety posters, banners, and reminders in common areas to keep safety at the forefront of everyone’s mind.
Encouraging reporting and feedback
- Establish an anonymous reporting system for safety concerns or incidents to encourage open and honest reporting, even if employees fear retribution.
- Create a feedback loop that acknowledges reports, provides timely responses, and communicates actions taken in response to safety concerns. Provide constructive feedback and coaching for negative safety behaviors and outcomes.
- Involve employees in safety committees or teams to give them a voice in shaping safety initiatives and policies.
- Provide easy and accessible channels for employees to report hazards, incidents, near misses, or suggestions for improvement.
- Acknowledge and reward positive safety behaviors and outcomes.
- Share information and best practices on safety issues. Seek feedback and suggestions for improvement. Communicate and collaborate with external stakeholders such as regulators, customers, suppliers, contractors, or community members. Establish clear expectations and standards for safety performance.
Efficient Employee Training, Communication, and Collaboration:
Training is essential for ensuring that your employees have the knowledge, skills and attitudes to perform their tasks safely and prevent accidents. However, training can also be costly and time-consuming, especially if you have a large or dispersed workforce. How can you optimize your training resources and deliver quality education to your employees?
Peer-to-Peer Training
- Encourage experienced employees to mentor new hires or less-experienced team members in safety protocols and best practices. This peer-to-peer approach can be a cost-effective way to share safety knowledge.
- Create a “buddy system” where employees work together to reinforce safety practices.
- Encourage experienced employees to mentor and train their colleagues.
- Develop a structured mentorship program and assign responsibilities to facilitate this process.
Utilize Innovative Training Solutions
- Utilize online training platforms and e-learning resources that can be cost-effective and accessible, allowing employees to learn at their own pace. Online training can reduce travel costs, increase flexibility and accessibility, and provide interactive and engaging content.
- Implement video conferencing tools for remote or virtual training sessions to minimize travel and training costs.
- You can use a variety of online tools, such as videos, quizzes, simulations, games, etc., to deliver your safety messages and test your employees’ understanding.
Safety Challenges and Competitions
- Organize friendly safety competitions and challenges among teams or departments to encourage collaboration.
- Offer small rewards or recognition for participation and winning teams to motivate employees.
Regular Safety Meetings
- Conduct regular cross-functional safety meetings to share updates, discuss safety initiatives, and brainstorm cost-effective solutions.
- Ensure that action items are assigned, tracked, and reviewed to promote accountability.
- Conduct regular safety discussions with employees to communicate, address safety concerns, and provide feedback.
Maintain Documentations
- Maintain detailed records of safety measures, incidents, and improvements.
- Review standards and make necessary adjustments where required.
Cross-Functional Collaboration
Another way to enhance safety performance with limited resources is to leverage the expertise and resources from various departments or functions within your organization. Cross-functional collaboration can help you access diverse perspectives, skills, knowledge, or tools that can help you address safety challenges more effectively and efficiently.
Leveraging expertise from various departments
- Encourage cross-functional safety teams or committees that bring together representatives from different departments.
- Tap into the knowledge and insights of these diverse teams to identify safety risks, share best practices, and implement comprehensive safety measures
- Identify common goals and interests for safety improvement. Align your objectives and strategies with the overall vision and mission of your organization. Find areas of synergy or complementarity where you can work together to achieve better results.
Collaboration for resource optimization
- Collaborate with departments to share resources and expertise. For example, maintenance and safety can work together to streamline preventive maintenance schedules and reduce costs.
- Identify cost-saving opportunities by sharing equipment, tools, or conducting joint safety training sessions to maximize the value of limited resources.
- Collaborate for resource optimization. Pool your resources such as budget, time, equipment, or personnel to implement safety solutions or initiatives. Seek opportunities to share costs or benefits of safety investments or interventions. Negotiate or trade resources based on your priorities or needs.
- Collaborate for innovation and learning. Exchange ideas and best practices on safety issues or solutions. Seek feedback or advice from experts or peers from different functions. Learn from their experiences or challenges. Experiment with new or alternative approaches to solve problems or improve processes.
- Ask employees, including maintenance personnel, to actively support the company in achieving health and safety objectives when resources are limited.
- Encourage maintenance personnel to maintain their machines well and keep them safeguarded to prevent breakdowns and downtime, thus helping the company efficiently manage limited resources and prevent losses through accidents.
Implement a proactive maintenance program for safety equipment to ensure its reliability and longevity. Train employees on proper equipment care and conduct regular inspections to detect issues early and prevent costly breakdowns.
Behavior-Based Safety: Inexpensive Strategies for Positive Change
Behavior-based safety (BBS) is a proactive approach to preventing workplace accidents and injuries by focusing on the human factors that influence behavior. It is particularly valuable when resources are limited because it emphasizes cost-effective and often zero-cost strategies to drive positive change in safety performance. BBS aims to identify and eliminate the root causes of unsafe behavior, such as lack of awareness, motivation, feedback, or reinforcement. BBS also involves engaging workers in observing, reporting, and correcting unsafe behaviors, as well as rewarding and recognizing safe behaviors. Here’s an explanation of Behavior-Based Safety and some cost-effective or zero-cost strategies:
Employee Involvement:
Cost: Zero or minimal
Encourage employees to actively participate in safety programs and to take ownership of their safety. Their involvement costs little but can have a significant impact on promoting safety awareness and encouraging safe behaviors. Involve workers in the BBS process from the start. Workers are more likely to adopt and sustain safe behaviors if they feel ownership and responsibility for their own safety and that of their peers. You can solicit their input on the safety goals, criteria, and measures, as well as involve them in conducting behavioral observations and providing feedback.
Behavior Observation and Feedback:
Cost: Zero or minimal
Encourage employees to observe and report safety-related behaviors. This can be done informally and integrated into regular work routines. Feedback mechanisms can be established to facilitate peer-to-peer feedback.
Regular Safety Meetings:
Cost: Minimal
These meetings can be facilitated by internal safety champions or employees. You can also use regular toolbox talks to discuss safety issues, challenges, and low cost solutions.
Safety Committees:
Cost: Minimal
Establish safety committees within the organization, composed of volunteers from different departments. These committees can meet regularly to discuss safety issues, share ideas, and develop safety initiatives.
Data Analysis:
Cost: Minimal
Analyze observation data and incident reports to identify trends and areas of improvement. This analysis can be done using standard office software. Use existing data sources to identify and prioritize the most critical safety issues. For instance, you can analyze injury records, near-miss reports, inspection results, or employee surveys to find out where the most frequent and severe incidents occur, and what behaviors contribute to them.
Visual Communication:
Cost: Minimal
Leverage existing communication channels to promote and reinforce safe behaviors. Utilize visual aids such as posters, infographics, newsletters, bulletin boards, intranet sites to share safety tips, best practices, success stories, or recognition awards and digital displays to reinforce safety messages. These can be created in-house at a low cost.
Job Safety Analysis (JSA):
Cost: Minimal
Encourage employees to perform JSAs as part of their daily routines. JSAs involve assessing and mitigating risks associated with specific tasks.
Collaboration with Suppliers and Partners:
Cost: Minimal
Collaborate with suppliers, partners, or industry associations to share safety best practices, training resources, and ideas without incurring significant costs.
These cost-effective and zero-cost strategies in Behavior-Based Safety can make a substantial difference in safety performance, even when resources are limited. Behavior-based safety is not a one-size-fits-all solution; it requires customization and adaptation to fit the specific needs and context of each organization. However, with some creativity and resourcefulness, you can implement a BBS program that is both effective and affordable.
Reward Announcement for Safety and Resource Conservation Champions
Recognize and celebrate safety milestones and improvements to boost morale and motivation. Rewarding your employees who save company resources and manage safety is a win-win strategy for your business. It can boost your employee morale and productivity, reduce your operational costs and risks, and improve your brand image and customer loyalty. By following the ideas and tips we shared in this blog post, you can design and implement an effective reward system that motivates your employees to save company resources and manage safety.
Here are some of the benefits of rewarding your employees for these actions:
- It can increase employee engagement and satisfaction, as they feel recognized and appreciated for their contributions.
- It can promote a culture of resource efficiency and safety awareness, as employees become more mindful of their actions and their impact on the company and the society.
- It can reduce operational costs and risks, as employees use less energy, water, materials, and equipment, and avoid accidents and injuries.
- It can enhance your brand reputation and customer loyalty, as customers prefer to do business with companies that are environmentally and socially responsible.
So how can you reward your employees who save company resources and manage safety? Here are some examples of rewards that you can offer:
- Monetary rewards: You can give bonuses, gift cards, vouchers, or cash prizes to your employees who achieve certain goals or targets related to resource efficiency and safety. For example, you can reward the employee who saves the most electricity, water, or paper in a month, or the employee who completes a safety training course or reports a potential hazard.
- Non-monetary rewards: You can also give non-monetary rewards, such as recognition, feedback, verbal praise, thank-you notes, certificates, badges, trophies, plaques or public recognition to acknowledge and appreciate safe behaviors to your employees who demonstrate resource efficiency. You can feature the employee of the month on your website or newsletter or give a shout-out to the employee who suggests a new idea or solution to improve resource efficiency or safety.
- Social or psychological rewards:
You can use You can also use team-based incentives, such as pizza parties, coffee breaks, or movie tickets, to encourage a sense of camaraderie and collective responsibility for safety.
- Experiential rewards: You can also offer experiential rewards, such as opportunities for learning, development, growth, or fun to your employees who save company resources and manage safety. For example, you can sponsor the employee who wants to attend a workshop or conference related to resource efficiency or safety or organize a team-building activity or outing for the department that achieves the highest resource efficiency or safety score.
The cost of rewards is but a fraction of the priceless achievements in safety
Managing Remote Work Can Reduce Cost of Safety Operations
Managing remote work can help reduce the cost of safety operations. The COVID-19 pandemic has forced many businesses to adopt remote work as a way to maintain their operations while ensuring the safety of their employees and customers. Remote work has many benefits, such as increased flexibility, productivity, and employee satisfaction. But can it also help reduce the cost of safety operations?
Safety operations are the activities that a business undertakes to prevent, mitigate, and respond to hazards and risks that may affect its employees, customers, assets, or reputation. These may include occupational health and safety, environmental protection, security, emergency preparedness, and compliance. Develop a basic crisis response plan for emergencies. Train employees on emergency procedures to minimize resource wastage during crises. Safety operations can be costly, as they require investment in equipment, training, monitoring, auditing, and reporting.
Remote work can potentially reduce the cost of safety operations by reducing the exposure of employees to physical hazards and risks in the workplace. For example, remote work can reduce the risk of injuries from falls, slips, trips, ergonomic issues, or exposure to harmful substances. Remote work can also reduce the need for personal protective equipment (PPE), such as masks, gloves, or goggles. Additionally, remote work can reduce the environmental impact of commuting and office operations, such as greenhouse gas emissions, energy consumption, or waste generation.
However, remote work also poses some challenges and risks for safety operations. Remote work can also create new psychological hazards for employees, such as isolation, stress, burnout, or lack of social support. Furthermore, remote work can make it harder to monitor and audit the safety performance and compliance of employees and contractors.
- Reduced need for physical safety measures: Remote workers do not need to be physically present in a workplace, which means that there is no need to implement safety measures such as security guards, access control systems, and fire safety systems. A company that has remote workers may not need to hire as many safety professionals, which can save money on salaries and benefits.
- Reduced risk of accidents and injuries: Remote workers are less likely to be involved in accidents and injuries, as they are not exposed to the same hazards as workers in a physical workplace. For example, they are less likely to be involved in slips, trips, and falls, or to be injured by machinery or equipment.
- Reduced costs of managing safety programs: Managing safety programs for remote workers can be less expensive than managing safety programs for workers in a physical workplace. This is because there is no need to provide safety training or to conduct regular safety inspections.
- Reduced costs of purchasing safety equipment: A company that has remote workers may not need to invest in as much safety equipment, such as fire extinguishers and first aid kits, which can save money on upfront costs and maintenance costs.
In addition to these direct costs, managing remote work can also help to reduce indirect costs associated with safety, such as the cost of workers’ compensation claims and the cost of lost productivity due to accidents and injuries.
Overall, managing remote work can be effective way to reduce the cost of safety operations. By reducing the need for physical safety measures, reducing the risk of accidents and injuries, and reducing the costs of managing safety programs, managing remote work can help companies to save money on their safety budgets.
Rewarding others may cost little, but its impact can be immeasurable.
Seek out free or low-cost resources and training opportunities.
Here are some resources and training opportunities to manage health and safety:
- The National Safety Council (NSC) offers a variety of free and low-cost resources
- The Occupational Safety and Health Administration (OSHA) offers a variety of free and low-cost resources
- The Center for Disease Control and Prevention (CDC) offers a variety of free and low-cost resources
- The Environmental Protection Agency (EPA) offers a variety of free and low-cost resources
In addition to these government agencies, many private organizations offer free or low-cost resources and training opportunities to manage health and safety. Some examples include:
- The American Red Cross offers a variety of free and low-cost training courses, including first aid, CPR, and AED training.
- The National Fire Protection Association (NFPA) offers a variety of free and low-cost resources, including safety publications, online training courses, and a safety app.
- The American Society of Safety Professionals (ASSP) offers a variety of free and low-cost resources, including safety publications, online training courses, and a safety app.
- The American Industrial Hygiene Association (AIHA) offers a variety of free and low-cost resources, including safety publications, online training courses, and a safety app.
Here are some tips for finding free or low-cost resources and training opportunities to manage health and safety:
- Search online. Many websites offer free or low-cost courses, tutorials, and other educational resources.
- Check your local library or community center. Many libraries and community centers offer free classes and workshops on various topics, including health and safety.
- Look for government programs. Many government programs offer free or low-cost training to eligible individuals.
- Network with other professionals. Talk to your friends, family, and colleagues to see if they know of any free or low-cost resources or training opportunities. You can also attend networking events to meet new people and learn about new opportunities.
Please note that some of these resources may charge a fee for access or for certificates of completion. Read the terms and conditions carefully before registering for any courses or programs.
By taking advantage of the free and low-cost resources and training opportunities available, you can learn the skills you need to manage health and safety effectively. This can help protect yourself, your family, and your colleagues from accidents and injuries.
“Connecting with fellow organizations to exchange ideas and industry best practices in health and safety, especially in resource-constrained environments, fuels a shared commitment to a safer, more efficient future.”
Strategic Safety Planning for Future Excellence in Health and Safety
Despite having limited resources, you can still research and write plans for your future safety practices. This is a good time to explore different options and strategies that can help you prevent or mitigate potential risks. You can compare and contrast different approaches and evaluate their feasibility, effectiveness, and cost. By doing this, you will have a clear vision of what you want to achieve and how you can achieve it. You will also be prepared to implement your plans when you have enough money and resources. Writing plans for your future safety practices is not only a productive way to use your time but also a proactive way to protect yourself and others from harm.
However, even when resources are limited, dedicating time to research and develop plans for future safety practices is crucial. This proactive approach ensures that when the time comes and financial resources become available, you are well-prepared to implement the best safety practices.
Understanding the Value of Safety Planning
Planning is an essential aspect of any successful endeavor. It allows you to anticipate potential challenges, allocate resources effectively, and set clear objectives. In the context of safety practices, planning helps identify potential hazards, assess risks, and develop strategies to mitigate them.
Research: The Foundation of Effective Planning
Research is the cornerstone of effective planning. It involves gathering information about current safety standards, emerging technologies, and best practices in your industry. This knowledge provides a solid foundation for developing plans that are not only effective but also align with industry standards.
Making the Most of Limited Resources
Limited resources can be challenging, but they don’t have to be a roadblock. By prioritizing your efforts and focusing on the most critical aspects of safety, you can make significant progress even with limited resources. Additionally, exploring cost-effective solutions and leveraging technology can help maximize the impact of your efforts.
Getting Ready for Future Implementation
Once you have developed your plans, you must keep them updated and ready for implementation. This means regularly reviewing and revising your plans to ensure they remain relevant and effective. When the time comes and financial resources are available, you’ll be in a strong position to implement the best safety practices swiftly.
Pro Tip: Even when resources are limited, taking the time to research and plan for future safety practices is a wise investment. It prepares you for future opportunities and ensures that you can implement the best safety measures when the time is right. Remember, planning today lays the foundation for a safer tomorrow.
Conclusion-Manage Health and Safety with Limited Resources
In conclusion, this article has discussed the impact of resource limitations on safety and how safety professionals can cope with this challenge. It has shown that resource constraints do not have to compromise safety standards as long as safety professionals adopt a strategic mindset and use the available resources wisely. Some of the strategies that can help achieve this goal are:
- assessing resource constraints
- understanding the impact of limited resources
- strategic safety planning and road mapping
- prioritizing the most critical risks,
- optimizing resources and safety investments
- collaborating with other stakeholders,
- Behavior-based safety strategies
- leveraging technology and safety training, and
- promoting a positive safety culture
- future planning for safety excellence
By applying these strategies, safety professionals can ensure that their organizations remain compliant, productive, and safe despite resource limitations. Therefore, it is essential for safety professionals to understand the impact of resource limitations on safety and to continuously seek ways to improve their health and safety management practices.
It is essential to reinforce the importance of adapting health and safety management to resource constraints. By encouraging safety professionals to apply the strategies outlined in this discussion and encouraging a commitment to continuous improvement, we can work collectively towards a safer work environment, even in the face of resource limitations. This proactive and strategic stance on safety management is key to maintaining a high standard of safety within resource-constrained settings, ensuring the well-being of all employees and the long-term success of the organization.
References:
https://www.osha.gov/safety-management/hazard-prevention
Frequently Asked Questions (FAQs)
If your question is not listed here, please contact us by filling out the form on the right.
Can’t find an Answer?
Join Our Safety Community!
Stay informed with the latest tips and insights on occupational health, safety, and the environment.
Thank you for addressing the important topic of managing health and safety with limited resources. This is crucial not only in workplaces but also in caregiving environments for seniors. Let’s continue to prioritize safety and well-being for our aging population, even when resources are constrained.
We appreciate you highlighting the importance of managing health and safety for seniors, even with limited resources. It’s a crucial aspect of caregiving that often faces challenges. Thank you for joining us in this effort!